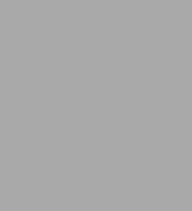
The Rocket Mass Heater Builder's Guide: Complete Step-by-Step Construction, Maintenance and Troubleshooting
288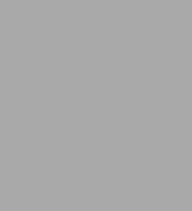
The Rocket Mass Heater Builder's Guide: Complete Step-by-Step Construction, Maintenance and Troubleshooting
288Paperback
-
PICK UP IN STORECheck Availability at Nearby Stores
Available within 2 business hours
Related collections and offers
Overview
A rocket mass heater is an earthen masonry heating system which provides clean, safe and efficient warmth for your home, all while using 70-90% less fuel than a traditional woodstove.
These unique and beautiful installations provide luxurious comfort year-round. In cold weather a few hours of clean, hot burning can provide 20 or more hours of steady warmth, while the unit's large thermal mass acts as a heat sink, cooling your home on sizzling summer days. Packed with hard-to-find information, The Rocket Mass Heater Builder's Guide includes:
- Comprehensive design, construction and installation instructions combined with detailed maintenance and troubleshooting advice
- Brick-by-brick layouts, diagrams, and architectural plans augmented with detailed parts drawings and photographs for clarity
- Relevant and up-to-date code information and standards to help you navigate the approval process with local building departments.
Earthen masonry heating systems are well-suited for natural and conventional builders alike. A super-efficient, wood-burning, rocket mass heater can help you dramatically reduce your energy costs while enhancing the beauty, value and comfort of your home.
Product Details
ISBN-13: | 9780865718234 |
---|---|
Publisher: | New Society Publishers |
Publication date: | 06/01/2016 |
Pages: | 288 |
Sales rank: | 305,073 |
Product dimensions: | 8.00(w) x 10.00(h) x 0.80(d) |
Age Range: | 16 Years |
About the Author
Ernie Wisner is a jack of all trades - his rich and varied background includes fishing and maritime work, firefighting, botany, natural building, hydraulics, and plumbing maintenance. Extreme conditions and high-risk work focused Ernie's attention on survival skills and emergency preparedness. After witnessing hard evidence of global climate change, Ernie's search for sustainable solutions led him to Cob Cottage Company, where he built his first rocket mass heaters while serving on the research team for Ianto Evans and Leslie Jackson's pioneering Rocket Mass Heaters . Together with his wife Erica, he has built over 700 super-efficient, clean-burning masonry stoves and led over 50 workshops across North America.
Read an Excerpt
Chapter 1 Rocket Mass Heater Overview and Terms
What is a Rocket Mass Heater? A rocket mass heater is a heavy, slowrelease radiant heater. It is designed primarily to heat people, secondarily to warm the areas in the line-of-sight around it. Modest tertiary functions include cooking, heating pots of water, and producing some warm air for distribution to other nearby areas.
A rocket mass heater is not a furnace or boiler; it should not be located in a hidden space, nor left to burn unattended.
The "rocket" in the name comes from a line of clean-burning cook stoves developed in the 1970s, using an insulated heat riser, to produce a very clean and efficient fire. "Mass" refers to the mass of masonry where it stores its heat. An RMH heater always includes an insulated, vertical, chimney-like heat riser as part of its clean-burning combustion chamber and a thermal mass to extract heat from its clean exhaust.
An RMH can warm a home using a fraction of the firewood required by other common heaters, such as woodstoves and boilers. The large, heat-storage mass these designs incorporate can heat multiple rooms from a central location, providing overnight heat without the danger and difficulty of an all-night fire. Rocket mass heaters are most effective in "line-of-sight" and by direct contact (built-in benches or sleeping platforms), although they do warm some air for heating distant rooms.
Not all builders of rocket mass heaters use the same design. This book shows our most popular "J-style" firebox design and a heat-exchange channel that incorporates a metal pipe liner. Alternatives are described in Appendix 3, such as bigger batch fireboxes, alternative thermal mass styles, and other successful experiments.
Like other rocket stoves, RMHs use a narrow, well-insulated fire chamber to maintain a clean, hot fire. Their "whooshing" sound during full burn is pleasant (and much quieter than a propane heater). The typical fuel used is any local, dried firewood - from small branches to split cordwood. Unlike cooking rocket stoves, which have a reputation for requiring finely-split fuels, a working rocket mass heater can burn any log that fits in the feed without further processing.
Many high-end masonry heaters require custom ceramic parts, but an RMH can be built with common metal components, firebricks, and locally available insulation and thermal mass materials. Because the mass is horizontal with low, even weight distribution, they are relatively easy to lay out and install. Comfortable surface temperatures allow these horizontal mass heaters to be installed and used in a wide range of situations.
The original rocket mass heaters (see Ianto Evans and Leslie Jackson's, Rocket Mass Heaters, 2006 and 2014) were designed and built using local, earth-based, recycled, and reclaimed resources. Most examples in this book show standard components, such as firebrick and stovepipe. However, reclaimed and site-sourced materials are used by many owner-builders; Appendix 1 gives details on earthen masonry and workable alternative materials.
The purpose of this book is to allow you to build a properly working example on your first attempt - without replicating known pitfalls. For clarity, optional features and specialized designs have largely been omitted, though there is some discussion of alternative designs in Appendix 3. We encourage new builders to build a proven heater design first, and learn its ways before making any design modifications.
Anatomy of a Rocket Mass HeaterParts and Functions
Combustion Unit
- Fuel loads vertically in the fuel feed. Air also enters here, controlled by a feed cover (not shown).
- Flames run sideways through the burn tunnel, then up the insulated heat riser.
- Together, the feed, burn tunnel, and heat riser make up the J-style firebox.
- Hot exhaust and fly ash fall down inside the downdraft bell/barrel , shedding radiant heat.
- The transition from this downdraft area into the heat-exchange ducts is called the manifold (see front cutaway view).
Parts and Functions
An RMH has two basic parts: the combustion unit and a heat exchanger. We will discuss the combustion unit first, and move on to the heat exchanger.
Combustion Unit
The combustion unit includes the fuel feed, burn tunnel, and heat riser (collectively the J-style firebox), and all the area under the bell (including the difficult-to-visualize shape under the barrel known as the manifold, which is the barrel-to-channel transition). The combustion unit experiences the hottest surface and internal temperatures. The right materials and correct proportions are critical for longevity, good draft performance, and clean combustion.
If a different type of combustion unit were substituted - one that did not burn as cleanly - there would be extreme danger of creosote buildup in the heat-exchange channels. In order to safely extract more heat from the fire's exhaust, that exhaust must be virtually smokeless. (When efficiency is the goal, a dirty fire is counter-productive anyway: smoke is wasted fuel.)
Combustion Unit Critical Functions
The role of the combustion unit is to create heat - and to do it cleanly. The flame path through the firebox interior must remain between 1000 and 2200°F (550 to 1200°C) for a clean burn. Consistently meeting this target despite the wide variety of natural fuels and weather conditions is not a trivial design problem; there may be damp willow and very dry oak or osage in the same woodpile. A firebox that reliably burns poor fuel above 900°F may occasionally exceed 2000°F with excellent fuel. (For reference, the temperature of flowing lava is often given as 1800°F; our clean fire can get hot enough to melt the Earth's crust.) To withstand a clean fire, we need special materials that are rated for thousand-plus-degree temperatures, known as refractory materials. Only clay-based brick or other suitable refractory materials should be used for the firebox interior.
Combustion Unit Components and Requirements
J-style Firebox
The fuel feed, burn tunnel, and heat riser together create a J-shaped path for fuel and flame. This narrow firebox or "J-tube" contains the flame path, similar to the firebox of a woodstove or other solid-fueled heaters.
Material: The firebox must be lined. Various materials can be used, depending on their "ratings," which indicate their ability to withstand heat. For a 6" heater in a moderate climate, materials rated for 2000 to 2400°F (1100 to 1300°C) are adequate, such as perlite-clay and common clay building brick. For cold climates, extended burn, or anything larger than 8" diameter, we prefer to line the firebox with materials rated for 2500°F (1350°C) or higher (firebrick, kiln brick, or rated refractory materials). Superinsulated fireboxes without a dense brick liner will reach hotter temperatures, and should be built of the highest-temperature materials available (high-end refractory insulation rated for 2800 or 3100°F (1530 to 1700°C), suitable for direct-flame exposure).
For proper draft performance, all the airflow channels in the system must provide the same cross-sectional area (CSA) - from fuel feed to exit chimney (with the exception of the barrel and manifold area, which may be larger). So, when building the firebox, you must create a consistent CSA. For example a system using 8" diameter exit pipe has a CSA of about 52 square inches, so the brick firebox channels are built to 7" by 7.5." See Chapter 6 for more on creating consistent CSAs.
Height: The hot, tall heat riser draws air and flames so strongly that it pulls air and flames down the relatively shorter, cooler fuel feed. This is the thermal siphon effect , making the combustion unit a thermosiphon. Like an ordinary siphon, this effect depends on differences in height and a complete absence of air leaks. Unlike a water siphon, though, the thermosiphon also depends on relative temperatures: hotter fluids move up, cooler ones move down. A hotter, taller heat riser works better. But a hotter or taller fuel feed can sabotage the draft.
Fuel Feed
This is the opening through which fuel and air enter the system; it is the first part of firebox. Fuel and cool air enter through the feed opening. The air strips heat from the top of the wood, reducing smoke-back and preheating the air. The fire burns hottest at the bottom of the feed. With good dry fuel, the sticks will burn all the way through at the bottom before the fire creeps up to their tops. They drop down as the bottom burns away, self-feeding and maintaining a bed of glowing charcoal for a steadier fire.
Fuel Feed Size: All fuel must fit within the fuel feed, so that the lid (not shown) can slide across for air control. Protruding sticks can cause smoke-back into the room. (See Chapter 5, Operation and Maintenance,for more details on fueling.)
The feed must be much shorter than the heat riser for the firebox to draw properly. Sixteen inches is a very practical height for the fuel feed (15"–16" is a common standard for cord-wood cutters). A 12" fuel feed is typically too short for locally available cordwood. The height of the fuel feed is related to the height of the heat riser. Our suggested 16" fuel feed requires a 48" heat riser, while a 24" fuel feed would require a 72" heat riser (6 feet tall).
Making a feed much larger than the system CSA requires a complete redesign of the firebox to prevent smoke in the room and creosote buildup in the chimney. See Appendix 3.
Durability: Normal fueling and cleaning can damage soft materials in the fuel feed and burn-tunnel areas. For this reason, we favor brick-lined fireboxes rather than pure refractory insulation.
Verticality: Natural wood fuels can selffeed downward for optimal air-fuel mixing and a steady burn rate, with minimal tending. The vertical feed, with its horizontal opening, also allows for an extremely cheap and effective fireplace door: two full-size firebricks can slide back and forth for air control or complete closure. (Half-size firebricks will get hot enough over a few hours' fire to toast bread, a nice bonus if you don't mind hot fingers.) With any fuel door capable of complete closure, it becomes the operator's job to remember that the fire needs air. The main burn usually runs best at quarter to half open (see Chapter 5, Operation and Maintenance).
If you need to shut things down before the fire is completely out, leave an air slot at least one quarter open (a 2" opening) at all times. Closing the air off completely will not only starve the fire, it may allow smoke to back up into the room as the stove cools down too early, or even cause a flash-back fire (explosive smoke re-ignition) if the smoke-filled box is re-opened while hot. Indoor heating fires are best extinguished by letting the fuels burn down in a controlled way, not by campfire methods like water or smothering.
Burn Tunnel
This horizontal section of the firebox allows flames to pass from the fuel area to the heat riser.
Coals often fall into this area to finish burning, and ash must be removed regularly during the heating season.
Some builders define the burn tunnel as only the area under the bridge (excluding the feed and heat riser areas). Our measurements are consistently given as the total lengths between the inside surfaces of the bricks, so the area we call the burn tunnel overlaps with the bottom of the fuel feed and heat riser.
Length: The minimum burn tunnel length is whatever is necessary to tunnel under the bell. With a smaller barrel or custom bell, the burn tunnel could be shorter without causing problems, but the bell must never overhang above the feed.
The feed bricks should be completely outside the bell, with at least ½" of crack-resistant detailing between them, and space to remove and re-build the feed bricks if needed. Ideally, we prefer a total of 4" to 5" thickness of masonry all the way around the metal bell, especially if the masonry is providing both structural connection and airtight, crack-resistant detailing. However, this longer burn tunnel requires a taller or hotter heat riser, which may be impractical under a standard 8-foot ceiling. To take up less space in the room, we can use a metal liner extending down into the masonry for air sealing, and snuggle the brick feed right up close to the metal bell.
The maximum burn tunnel length is not more than half the heat riser height.
Shape: Brick channels, with their slightly rough surfaces, give a cleaner burn than a smooth or round firebox. (J-tubes were originally prototyped using metal stovepipe, however in addition to the problems of less-clean burn, metal also warps, cracks, and burns away rapidly when repeatedly exposed to high-temperature heating fires.) A square cross-sectional area is easiest to build and manage. When square is not practical with a given brick dimension, next best is slightly taller than square, making it easier to clean out the ash. Using 9" firebrick to span the bridge creates a functional limit of about 7" to 8" burn tunnel width in any case, though this limit can be circumvented with other materials and methods.
Maintenance: The burn tunnel materials must withstand intense heat and periodic abrasion from ash-cleanup tools. Brick works well; softer refractory materials will degrade over time.
Bridge
The bridge is the ceiling of the burn tunnel, usually made with bricks or refractory slab.
Brick Replacement: The first brick in this bridge is part of both the fuel feed and the burn tunnel, where cool air and hot flame meet. This brick experiences intense thermal shock, strain, and damage from rough handling of fuel. Cracking is common. Allow for eventual replacement of this brick. We typically set this course and any feed courses that rest on it with a pure clay mortar, to allow for easy removal and resetting of all three bricks without rebuilding the entire firebox.
Many attempts have been made to extend the lifespan of this brick, but no alternative materials we've heard of have worked much better than a standard firebrick, which is also pretty easy to replace when needed. A full size firebrick will also provide many years of additional service despite a small hairline crack, while fancy solutions may fail in less-controlled ways and require earlier replacement.
Heat Riser
This is the engine of the system. The heat riser is the insulated, vertical channel that draws flame upward and powers the rest of the firebox. Insulation helps hold the flames at high temperatures for complete combustion. A colleague compared the effect to an intentional chimney fire that burns the whole time, converting harmful smoke and creosote into clean, efficient heat.
Heat Riser Height: The heat riser must be substantially taller than the fuel feed opening (at least three times taller, measuring from the floor of the burn tunnel to the top edge of the riser). It should also be about twice as tall as the burn tunnel's length; this means the heat riser is always longer (taller) than the fuel feed and burn tunnel lengths put together.
Temperature: For good draft, you'll need to keep the heat riser hot. Surface temperatures can be 2500°F during a roaring fire. This means metal is not appropriate in the interior of the heat riser (or anywhere in the firebox); it will warp, crack, and eventually burn back down to ore. Ceramic materials such as firebrick, clay brick, or refractory ceramic components are the best choices for a heat riser's interior surfaces. Refractory insulation (2" perlite or 1" refractory blanket) keeps the inside hot and the outside cool; the exterior of this insulation usually stays below 600°F, so galvanized metal can be safely used for support around the outside of insulated heat risers.
Insulation: The heat riser must be completely insulated for reliable draft performance. Without insulation, the updraft and downdraft surfaces of the heat riser equalize about half an hour into the fire. The draft stalls, causing smoke to choke the fire (and the operator).
Insulation can be monolithic, such as a cast heat riser of insulating refractory materials, or it can be made from the light, foam-like insulating kiln bricks. Our preferred construction is a heat riser made of durable, dense firebrick, insulated with 1" to 2" of suitable refractory insulation such as perlite, ceramic-fiber blanket or board, or high-temperature rock wool. See Chapter 4, Step by Step Construction Example.
Bell/Barrel
The bell is also called the downdraft bell, contraflow bell , or the barrel. It is the container that redirects hot exhaust from the heat riser down into the mass. Typically made with a metal barrel or similar capped cylinder, the weathered metal surface provides quick radiant heat to the room and facilitates downward draft by slightly cooling the exhaust that flows through it.
"Bell" in masonry heating is a technical term for a chamber that traps rising hot gases to extract their heat. For proper functioning, its flow area must be at least four times larger than the system CSA.The gases stratify in this large slow-flowing space, with the hottest gases at the top, and the coolest gases sinking and escaping through the outlet near the bottom of the bell. In a well-proportioned heater, these cooler gases are still warm enough to rise upward in the exit chimney.
In the case of rocket mass heaters, the space under the barrel is not exactly a full-sized bell - it could also be considered as an oddly-shaped contraflow channel, with streams of hot gases flowing down the sides toward the heat storage bench.
Size: The practical bottom line: In the barrel and manifold areas, flow areas from twice to four times the system CSA seem to work fine. Larger may be fine too; we have not yet seen any such thing as "too much space" in this area. Too small a space creates problems: if there is less than 150% of the system CSA - or less than 1.5" actual dimension between inner and outer surfaces - we see ash clogging and flow restrictions.
Complete Air Seal: Airtight, smokeproof sealing is the most critical function of the barrel or bell. Any joints must be double- sealed with gasketing, clamps, or other heat-resistant sealers such as mortars or stove cements. (See Appendix 5 for maximum operating temperatures and appropriate ratings for high-temperature tapes, cements, etc.) Pinhole leaks in the barrel are not acceptable.
Radiant Heat: The barrel's primary purpose is not to trap hot exhaust, but to keep it moving toward the heat-exchange mass. For this reason, the barrel must not be insulated. Radiant heat loss from the barrel cools the exhaust gases so they can draft downward in this area and keep the system drafting correctly. See Appendix 6 for decorative and heat-shielding options around the barrel/bell.
Manifold
A manifold is a weirdly-shaped space where many pipes or channels connect, like a car engine's exhaust manifold. The manifold in an RMH is the transition area connecting the area under the barrel to the heat-exchange ducting opening(s), usually with an ash cleanout. So we have gases entering through the cylindrical slot/barrel-rim shape above, and exiting below to reach the heating channel( s) and a cleanout access opening.
The manifold may be constructed with an airtight brick plenum (box) with appropriate metal fittings mortared in place; as a hollow cob or adobe cavity sealed with earthen plasters; or by using a metal form such as a partial barrel or a slot-to-round heating vent, mortared or cobbed in place.
Manifold Air Seals: Exhaust leaks or air leaks in the manifold can interrupt the downward flow in the bell, causing stalled draft. Plan around any difficult-to-reach areas for a good seal and easy maintenance. For example, with brick work we often see novice builders having difficulty making good mortar seals in the corner behind the firebox, where access is difficult; with a fabricated steel part, the edges and fittings are the obvious weak points in the airtight seal. Rather than chasing leaks with your nose or a CO detector, consider allowing an extra ½" of volume inside masonry manifolds to apply a crack-free earthen plaster inside. Better yet, consider finishing the exterior with a clay-based finish plaster, making any cracks very easy to detect and repair.
Manifold Area/Volume: The throughflow areas of the manifold need to be substantially larger than the system's crosssectional area: at least 150% where the exhaust is changing direction, and about two to four times larger where it's merely flowing downward. Watch for bottlenecks created by fly ash buildup on any horizontal surface. A large ash pit below the heat-exchange ducting can help reduce blockages.
Manifold Cleanout Access: Provide access for annual ash cleaning. The cleanout needs, at minimum, to allow a hand or vacuum brush to remove any fly ash or obstructions between the heat-exchange channels and the barrel downdraft areas. If there is an ash pit, the cleanout should be able to reach it too.
We always keep this cleaning access in mind as we build - you want to be able to reach into the manifold and pull your hand back out intact, and the difference between permanent structure and ash (sometimes hardened by years of neglect) should be clear even to gloved fingertips.
With adobe or cob manifolds, we sometimes build in a tile floor, or use a good hard plaster on the interior. Perlite insulation is easily mistaken for ash, and needs some plaster or tile reinforcement. With blanket insulation, we always provide a metal cage strong enough to hold the blanket against a vacuum nozzle's pull, and sometimes plaster this as well.
Cleanout access may be:
- a capped T in the first section of exhaust pipe
- a capped pipe or tile cleanout in the manifold itself (mortared into masonry manifolds)
- a removable barrel or barrel-lid, air-sealed with fiberglass woodstove gasket. (But lifting an entire barrel carefully over the heat riser every year will make you wish for an easier cleanout.)
Heat Exchanger
The heat exchanger includes the system of channels and masonry that capture exhaust heat: the heat-exchange ducting, thermal core, and casing. The most popular and efficient layouts are horizontal, creating a bench, bed, or heated floor.
Heat Exchanger Critical Functions
Thermal mass storage: To function as described, an RMH needs a large mass of dense material to store heat. The materials used vary. Metal, brick, clay, stone, or even water can all be used as heat storage mass. (Water, though, is a lively and weird heat-storage material with its own special challenges; see Appendix 3.)
The original rocket mass heater designs all used a clay-based earthen concrete called cob - and they used a lot of it. A typical rocket mass heater's masonry may weigh 3–6 tons (which is distributed on the footings at about 120–200 lbs/sf ). The transportation of such heavy materials is a large part of their cost and environmental impact, which is why we prefer to use materials from as close to the project site as possible (whether it's stone, cob, adobe, tamped mineral soils, or recycled concrete rubble).
Heat storage capacity for a given mass of material is measured by the material's heat capacity, weight, conductivity, and degree of temperature difference. It's possible to store the same amount of heat in less mass if you can get the mass hotter ... but the temperature of the small, hot mass will also drop more quickly, delivering that heat in a shorter time.
Airtight: The channels that carry exhaust through the thermal mass should be double-sealed to prevent exhaust leaks. The primary seal is created when building the channels from metal pipes, clay pipe or chimney liners, or mortared brick. A secondary seal is provided by wet-formed masonry in direct contact with these lined channels. If there is no wet-formed masonry around the pipe channels, then a reliable air seal must be provided some other way (for example, welding the pipes, and installing CO detectors).
Efficient Heating: Conductive heating is highly efficient. A full-body heating pad or heated seat keeps occupants deliciously warm, even at room temperatures cooler than normal. Radiant floors or low heated benches reduce stratification of room air; instead of hot air rising up to the ceiling and looking for ways to escape the house, more warmth stays down where it's most useful, resulting in greater overall comfort and less wasted heat.
Safety (structural and fire/exhaust): The thermal mass bench must be airtight to prevent smoke leaks and control any condensation/drainage. It must remain structurally sound through decades of use, possibly including earthquakes, floods, and changes of family life. Structural integrity must carry through both the core and casing.
Insulation Note:
Some people think insulation "stores heat" or "keeps things hotter." But, as it goes with a Thermos, insulation can also keep things colder. What's going on? Insulation actually blocks heat transfer. The insulation itself typically doesn't hold much heat, being mostly air, so it prevents heat from reaching anything on the other side. Thus you typically don't want to put insulating materials between the exhaust pipes and thermal mass, or within the thermal mass; this would stop your heat from reaching its storage (and you!). Insulating materials to watch out for in the thermal mass core include hollow straw, and any material with empty air pockets (loose sand, gravel, sloppy filling around the pipes, etc.). Insulation is sometimes desirable around the outsides of the mass, to prevent heat transfer (for example along an exterior wall), or as removable cushions that trap and control the stored heat for later use (for sleeping cool, then tucking toes under the cushions next morning). A small amount of straw or fiber in the outer casing can be useful for other reasons.
Heat Exchanger Components and Requirements
Channels
Lined channels carry the warm exhaust through the mass, transferring heat through the channel walls into the storage mass. Using standard metal pipes makes it easier to lay out and set slopes for these channels, but channels can also be built with any material that will tolerate the heat, damp and corrosive exhaust, and occasional abrasion from cleaning: clay chimney liner, clay drain pipe, or smoothly-mortared brick.
Consistent Cross-sectional Area (CSA):
From manifold to chimney, all the ducts are the same cross-sectional area. Ideally, the areas connect smoothly, without corrugations or obstacles to induce turbulence, and the channels are shaped as circles, rounded squares, or other similar shapes that allow excellent through-flow.
Heat-exchange Duct Length: The heatexchange channels extract and store useful heat, but they also represent a load on the system's draft (through friction and cooling). A 6" or 8" diameter system typically has 20 to 40 feet of ducting length, and at least one 180-degree turn. There is no practical minimum length, but a shorter system will store less heat and may exhibit over-drafting (drawing too much air for the fire). See Chapter 6 for specific rules of thumb regarding length.
Orientation: Roughly horizontal layouts are the norm; they distribute weight loads and offer maximum comfort seating. We slope the pipes upward slightly, ¼" over 8 feet or so, or about 1" over the whole run in a level bench. This slope allows for upward gas flow, downward drainage of condensation water to a cleanout, and provides even heating on the surface by locating the hottest pipes lower and the cooler pipes closer to the surface.
Where a vertical configuration is needed to fit the space, channels should run roughly horizontal or with a slight rise between turns, just as in a horizontal bench. Avoid zigzagging up-down runs because they trap hot and cold air, causing substantially more draft resistance and inconsistent heating.
Smooth Inner Lining: Only smooth, easily-cleaned materials should be used to line the heating channels. Rough or corrugated textures can create drag equivalent to tens of additional feet of length per foot , seriously affecting the system draft. Avoid corrugated pipe, wrinkly corrugated elbows, wrinkly flexible ducting, or chimney-liner sections with spiral corrugations. Adjustable elbows that rotate are smooth enough to work well, and T's for cleanouts seem to have little effect on drag. Large voids, such as cleanout extensions through an exterior wall, may affect draft.
Maintenance: As in the combustion unit, all linings should be durable enough to tolerate manipulation of a brush, drain snake, or Shop-Vac hose.
Capped Cleanouts: Cleanouts need to allow maintenance access to every part of the system. Critical cleanouts are located at each 180-degree bend and at the bottom of each vertical drop such as the barrel/ manifold and the exit chimney. Any series of 90-degree bends may also need additional cleanouts to give access to each pipe. Imagine using a periscope mirror and flashlight to try and find an asphyxiated squirrel in there, and make it easy.
Fresh Air Separation: If any channels are built to convey outside air or room air, these must be completely separate from the exhaust ducting channels. Be extra careful in any areas where an exhaust leak would be hard to inspect, such as the wall side or interior of the heater.
The exit chimney opening should likewise be located outdoors, above the roof ridge, a suitable distance from any nearby air intakes, doors, or windows.
Thermal Mass
Thermal mass refers to all the masonry surrounding the heat-exchange ducting, including the core and the casing.
Density/Heat Storage: Thermal mass is dense so it can store more heat over hours or days. Light, foamy, or airy materials block heat transfer and have less heat-storage capacity.
Reactivity: Thermal mass materials should be nontoxic, chemically resistant or inert. They should not corrode or degrade if exposed to exhaust leaks or minor water damage, and be completely unaffected by moderate heat. The hottest areas are immediately around the firebox, manifold, and first run of heat-exchange ducting. Temperatures of the interior mass in these areas may exceed 500°F during operation, with surface temperatures up to 250°F.
Conduction, Not Insulation: Airy materials such as perlite, pumice, straw, and dry sand offer insulation, not heat storage. Insulation may be useful between thermal mass and exterior walls, but not within the mass itself. Thermal mass should be relatively dense and conductive, the opposite of insulation. If airy or light materials are included in the mass (either to reduce weight, or in a misguided attempt to save the heat), they will reduce the heat transfer and heat-storage capability of the mass.
Core, Thermal Cob
This is the dense material that surrounds the channels of the heat exchanger. Usually it is earthen masonry or fireclay-mortared unit masonry. It is the permanent structure around the ducting, and provides the immediate heat transfer and most critical heat storage mass.
Secondary Seal: The core of the heater provides the secondary seal and heat-transfer functions around the heat-exchange ducting. The ducting may last for decades, but good masonry detailing here can last for centuries. If you notice any voids, cracks, or crumbling areas in the core materials as they
dry, these cracks should be patched, or the faulty material should be removed and replaced before finishing the casing.
Heat Conduction: Core materials should be fairly conductive - comparable to brick or earthen masonry, which transmits heat at about 1" per hour. If using an infill technique (such as described for greenhouse heaters or some portable designs), try to find mixed, small aggregates such as ¾"-minus rock-crusher gravel or quarry fines, masonry sand, or a suitably gravel-rich natural mineral soil. Avoid sifted sand, beach sand, perlite, or other uniform and air-trapping materials.
No matter the size of the particles, mixed sizes and sharp edges are easier to pack and stack, and dense packing gives better heat storage. (Four loose buckets of good masonry sand plus 1 bucket of clay might make 2.5 packed buckets of fill material - it gets a lot denser as you mix.) A mess of identical round sand grains or river rocks are hard to stack, and it will take a lot of clay, mortar, or fill materials to fill those air pockets or they will block heat transfer.
Infill: The core of the bench can incorporate any available masonry rubble including concrete chunks, rock, gravel, even pottery shards or broken dishes. Avoid dangerous materials such as broken glass, vacuum tubes (strange but true, people have buried old TVs in cob projects - repair crews beware!), contaminated factory wastes, or heat-sensitive/ flammable materials.
Casing
Also referred to as cladding or veneers, the casing is the final, outer layers of the heat-exchange mass and the supporting masonry around the combustion unit. Typical casing materials include earthen plaster, stone, brick, tile, and some other materials that offer a durable and attractive finish. Some builders have used wood trim, but only in well-tested locations away from high-heat areas.
The casing can be built first and then filled (for example a brick box, with the ducting just 1" from the inside of the brick), built in courses tied into the heater's core (like rough stonework), or applied later as a finish layer (such as plaster or tile). Materials that could trap moisture are best applied after the core is completely dry. If the heater has been thoroughly test-fired while drying, these decorative materials can hide any patched cracks from the drying process or heat-expansion.
Durability: The casing materials should stand up to ordinary wear-and-tear. Normal use includes people sitting, sleeping, dining, dropping things, wrestling on the sofa, and climbing all over it like monkeys. Common variations might include sheltering and watering houseplants, using heat to quicken home brewing, quick step-ladder function to water hanging plants or change an overhead light ... possibly all simultaneously. Crayon-resistance is optional.
Repair or Refinish: Some materials are easier to repair than others (see Appendix 1). It is helpful to set aside color-matched plaster for later patching.
The best masonry heaters are designed for eventual piece-by-piece inspection and repair; they last longer because they can be fixed or remodeled as needed. Some modern masonry materials bond too strongly for practical repairs; instead of repointing soft mortar or grout, a crack in these modern materials may require complete replacement of broken bricks and tiles.
Moisture Protection: The heater should be well protected from damp, including ventilation and drainage of the heater base to dry out construction moisture. But don't try to waterproof the entire outer surface: trapped internal moisture can cause blistering or separation of the casing layer, or unsightly mineral blooms. Breathable, heat-tolerant finishes can be used to create a water-resistant, durable surface. Waxes, oil paints, and volatile oils generally are not suitable for heated surfaces.
See Appendix 1 for more detail on natural plasters and other compatible finishes.
Heat Tolerance: Operating temperatures for the heat-exchange mass itself tend to range between 70–100°F for room heaters (20–40°C), or up to 150°F (65°C) for larger house heaters. Combustion unit temperatures and some high-output designs may have higher surface temperatures (up to 250°F/120°C).
Natural wood trim can be used on areas that never exceed 150°F (65°C) in the heaviest use. Natural fibers can be included in mineral plasters (clay, lime, gypsum plasters) without making the plaster combustible.
Fabric Choices: Natural-fiber fabrics and battings that tolerate warm or hot settings on an iron or tumble-dryer (roughly 300 to 400°F/150–200°C) are suitable for most heat-exchange benches or beds. Remember that cushions are insulation; heat trapped underneath cushions can raise the surface temperature of the masonry higher than if it were bare. Check to make sure all surface temperatures in contact with wood, fabric, cushions, or other combustible materials remain below 150°F (65°C) - not painfully hot to touch. An isolated hot spot can be covered with thicker masonry (tile, plaster, or a sculptural element such as an arm-rest over the hottest areas adjacent to the barrel). Or you could add another inch or two of tile or plaster to the whole bench, to absorb some of the excess heat.
Exit Chimney
The exit chimney is a sealed pipe or flue that conveys exhaust out of the building. Proper chimney design helps ensure good draft for the heater, despite varying wind and weather. Most installations use a standard manufactured chimney, a low-temperature appliance exhaust, or a lined masonry chimney.
Draft: Vertical, warm chimneys provide draft that keeps the whole system operating smoothly, and provides a slight under-pressure to prevent smoke escaping any pinhole leaks. Unconventional chimneys often cause draft problems.
Structure: Chimneys should be physically self-supporting independent of the heater itself (in case of building problems, refits, or repairs).
Maintenance: Chimneys should have a cleanout near the bottom of the vertical section, an appropriate rain cap and screen (with through-flow area of at least 100% of system area).
Wind and Weather: The simplest and most reliable options are generally dictated by local building codes and best practices for combustion appliance exhaust and woodstove chimneys. Wind gusts, snow loads, ice dams, rain, prevailing winds, seismic loads, differential frost heave or settling of buildings, and variable outdoor temperatures create special problems for chimney design.
The easiest place to make a chimney exit weatherproof is actually near the ridge top, where there is less rain and snow coming down the roof toward the installation, and it's easier to lap the chimney flashing over any type of roofing. This also allows the building's rafters or trusses to support most of the chimney, while raising it to the proper height above the gusting chaos of building-related wind eddies.
Temperature: Woodstoves must exhaust above 350°F by law in the US (about 175°C, but local laws vary). Fireplaces and woodstoves often exhaust as hot as 600–800°F (300 to 450°C). Masonry heaters generally exhaust between 200–400°F (90 to 200°C). Rocket mass heaters can draft substantially lower, as low as 60°F (15°C) in some odd cases outside the realm of normal building practice.
Some efficiency-minded colleagues glory in seeking out the absolute minimum exhaust temperature. A few of Evan's original heaters ran fog-like exhaust well below its dew point at 60 or 70°F (15 to 20°C). This is very exciting for efficiency fans, as almost no heat is being lost outside the building. Unfortunately, this exhaust emerges as a cool, dense fog that will not rise in a conventional chimney, and it lacks the force to overcome even the slightest wind pressure. These ultra-low-temperature exhausts must exit nearly horizontal or downward, and are difficult to protect from normal wind and household pressure conditions. Too-low exhaust temperatures create draft problems in almost all conventional buildings, and are especially unreliable in winter storm conditions (just the time when an electrical exhaust fan is also vulnerable to power failure).
The only conditions in which a balky heater with a tendency to run backwards would be acceptable are conditions where winter heating is not critical for survival - and in those cases, passive solar heat collection and a smaller, seldom-used wood heater would generally be a more practical and more energy-efficient solution.
For reliable draft and efficiency, we generally target a surface temperature of 100–150°F (40–65°C) on the exposed exit chimney pipe during test-firing. Average exhaust temperatures inside the pipe are likely close to 200°F/90°C, the low end of masonry heater exhaust).
For further discussion of best practices, see Chapter 4, Step by Step Construction Example and Appendix 3, Alternative Chimneys.
Major Design Considerations
Here are some general "rules of thumb" to follow when installing a rocket mass heater. These rules are covered in detail in Chapter 6. However, a few key points may be important at this stage.
Cross-sectional Area (CSA): The basic rocket mass heater designs use the same cross-sectional area for all channels, with the exception of the downdraft barrel and manifold (which may be larger).
Combustion Area Proportions: The heat riser height drives the whole system's draft. The heat riser should be at least three times taller than the fuel feed, and at least twice as tall as the burn tunnel length.
As an example, an 8" heater that meets these proportions might have a 16" fuel feed, a 24" burn tunnel, and a heat riser 48" tall. The heat riser could be taller (up to about 6 feet) but not shorter.
Length of Heat-exchange Pipes: The goal is to extract as much heat as practical, without making the system too cold for comfort or too difficult to start. Climate, heat load, and available space all factor into the desired size of mass. The mass and pipe length are not the only load on the system draft: the number of turns, rough texture of pipe, or other obstacles to smooth flow will greatly reduce the draft and a shorter pipe may be needed to compensate.
A typical heat-exchange bench runs about 20 to 35 feet of heat-exchange channels, with one or two 180-degree turns, for a cool-climate exhaust that runs about 100 to 150°F (pipe exterior temperature).
For hotter climates or trickier operating conditions, a shorter bench and a hotter exhaust (200–250°F) may give more reliable draft. A heater with horizontal channels between 12 and 20 feet in length will exhaust in this hotter temperature range. The sacrifice in fuel efficiency is only about 10%.
So if you have a variable heating season (such as not heating if you're gone on vacation), the climate is hot or variable, you are not able to store two years' supply of dry wood, or you want to be able to operate the heater in warmer weather for saunas or visitors, consider a shorter bench run.
A poor exit chimney (cold, less than half the building height) is a tremendous obstacle to good draft. The condensation of water in the exhaust can cause chimney stalls, which helps explain why cold, exposed outdoor chimneys often draft poorly, even if they never become actually colder than outdoor air.
Detailed rules of thumb, building codes, and workable proportions are given in Chapter 6: Rules and Codes.
Is a Rocket Mass Heater Right for Me?
What Rocket Mass Heaters Are and Aren't
Rocket mass heaters are large space heaters, typically installed in a central part of an occupied home. In the right location, they are extremely efficient. In the wrong setting, they are a waste of effort.
- They provide steady, ongoing heat. They work best in a continuously-occupied home (as opposed to a weekend cabin or chapel).
- Rocket mass heaters are not automated central heating. They do not replace a furnace or boiler; they are not designed to run unattended in a basement. Instead, they are a form of gentle radiant heater, and they perform best when centrally located in the occupied space. Many owners find that their rocket mass heater substantially offsets the furnace bills, and heats several adjacent rooms nicely, but the heat may not evenly reach the farthest rooms.
- Human Operated: For reliable heat in case of grid power failures, our designs are fully manual, no electric automation. This means a human operator must supervise the fire.
- Unusual: Local officials may have no idea how to permit or inspect one, and insurance companies may need to be approached (and educated) about coverage. There is a learning curve for operating a downdraft heater, as the fire is upside down compared to most woodstoves or fireplaces.
- Site-specific design and installation implies local knowledge and intelligent choices. Unique designs are more common than any standard model. When building in a new situation, it's possible that under those new conditions, an identical heater will not function as described here.
- Finally, the designs in this book are intended to burn only natural wood fuel such as brush, branches, poles, small logs, split cordwood, lumber scraps, and small amounts of other natural fuels such as paper tinder. For examples of alternative fuels designs, see Appendix 3.
Considerations
Benefits
An RMH provides efficient heating that matches the needs of many American households, especially for a primary residence. They offer safe warmth overnight; efficient use of local, renewable resources; and affordable, DIY-friendly construction and maintenance. Rocket mass heaters do not duplicate the (inefficient) functions of a furnace or boiler. Part of the way they save energy is by heating people instead of space. (See in Chapter 2, "Heat Transfer" for details.)
To achieve the best possible results, these systems rely on locally available materials, knowledge, and fuels (ideally waste or thinned fuels, not standing timber).They offer simple and satisfying operation and maintenance, and low construction costs (competitive with a new woodstove). When properly constructed they will produce a clean fire (no creosote or wasted fuel).
Most masonry heater designs share these goals of safe warmth and fuel efficiency, and many achieve similar clean burning and heat storage. However, most masonry heater designs of comparable capacity are more expensive to build due to cast-ceramic parts, metal and glass doors, fancy veneers, and other popular design elements. Each style of masonry heater has its own special design rules and tolerances. (See The Book of Masonry Stoves , by David Lyle.)
The designs we use were developed within North American culture, specifically within a grassroots community of self-sufficiency enthusiasts. Rocket mass heaters are attractive to this community because they offer grid-independent or off-grid heating, and they are good alternatives for single-family or single-occupant homes whose owners are busy and have limited hours to tend the fire. They also offer a quick return on investment. This is important in our context because, on average, Americans move their households every five years.
We can hope, but we do not confidently expect more than five years' return on any investment in home improvements.
Some Pros and Cons
Convenience at modest cost comes with some downsides. Here is a quick review of some pros and cons of RMH heaters:
Pro : Quick payback. Fuel savings will often repay installation costs in less than four years - often less than one year for resourceful scroungers replacing inefficient heaters.
Con: The most effective, cheap materials are not always the prettiest, and there can be conflicts with local building codes.
Pro : Rocket mass heaters are routinely built by novice masons and owner-builders. Expert help that might be available could include interested heater masons, natural building contractors, and heating engineers; such professionals may be able to help with projects challenges, including local legal questions.
Con: Work done by non-professionals may be less acceptable to local decision makers. Owner-builders often have more legal freedom than landlords, mortgage-holders, or renters.
Pro: Materials are readily available. Commercial, reclaimed, or recycled parts and local mineral materials may be used for mass.
Con: Using reclaimed or site-sourced materials may not be permitted under building codes; upgrading to new, modern materials may involve unexpected costs. Using sitesourced materials effectively takes some skill and practice.
Pro: Heat output is both steady and responsive. A traditional masonry heater requires 12- to 24-hour advance operation. A woodstove heats instantly, but cools just as quickly. Rocket mass heaters provide quick radiant heat from the metal bell, and steady stored heat from the bench: best of both worlds.
Con: The metal bell's radiant heat can overpower a small room during extended firings; all-masonry heaters may heat more evenly. The bench takes time to heat up after an absence, and will also store heat even if not wanted (such as if you fire it up to cook in summer).
Pro: Rocket mass heaters are not dependent on power grids or imported sources. Heater self-regulates to a degree, but rewards conscientious operation.
Con: You may need a house-sitter during winter vacations to light the stove two or three times per week, if you need to keep plants and plumbing intact in cold climates. If your sitters can't be trusted or trained, you'll rely on other options like an old but working furnace, heat-tape for the pipes, or using frost-free plumbing design.
Drawbacks
They Take Up Space
Rocket mass heaters do fit into a surprising variety of situations, having simpler foundation requirements, more flexible design configurations, and lower heights and clearances than many other masonry heaters. But they still take up a substantial amount of space.
Most North Americans use hidden furnaces or a compact (if uncomfortable) woodstove. Modern homes may not have an ideal space for a mass heater. Traditional masonry heaters are often built first, then the house is built around them. A well-integrated masonry heater can serve as a dividing wall to warm three or more rooms, and other nifty features can be added. Retrofitting these features into an existing space is trickier.
The optimal place for effective heating is to locate the heater wherever you sit the most; you can replace the woodstove plus your favorite sofa. If that's not possible, consider a new dividing wall or section of floor (with the heater mass sunk into the crawl space). The most effective heating location is therefore, unfortunately, the one that will most disturb a beloved hangout spot.
Change is not fun, and living in a construction zone is not fun, so consider domestic tranquility in your planning. It may be less disruptive to build the heater into a new addition on the house, even if the resulting heat is less efficient than with a centrally placed heater. Or, your rocket remodel could redefine the favorite hangout spot, turning an under-used space or bump-out into the hot new hangout spot.
Non-standard Technology
In this era of global appliance manufacturing, site-built masonry heaters may be rare in your area. Local officials, co-owners, mortgage lenders, and others may need time to get used to the idea.
Do you need approval for your project? Mortgage or insurance contracts may impose strict penalties if you build your own heater without official approval. Some owners have had success getting local permits, or discovering applicable exemptions; others have run up against weird local regulations or skeptical building officials.
See Chapter 6 and Appendix 2 for more about local codes.
Learning Curves Can Be Steep
While the vast majority of owners have little trouble adapting to their new heaters, it may be a different story for guests or new tenants. Contractors unfamiliar with the design may introduce almost as many problems as they solve. Well-meaning visitors can have a great deal of trouble guessing how to correctly operate the heater.
If possible, visit others' heaters during the heating season, or build a prototype in an outbuilding. Nothing convinces the household holdouts like the experience of sitting on the warm bench in chilly weather.
Loading Takes Time
A rocket heater can only burn so much fuel in a day, or in the available hours that people can watch the fire. But the fire should not burn unattended - though the operator can easily combine fire tending with other routine activities nearby. Keep an ear or eye on the heater from any nearby room, refueling or adjusting the fire every hour or two. Hours of operation vary with heating load.
In modest, well-insulated homes (up to about 1500 square feet), an 8" system might burn:
- 1 to 2 hours per day in cool/mild weather (30–60°F/0–15°C)
- 4 to 6 hours per day in chilly weather (0 to 30°F/-15 to 0°C)
- 8 to 10 hours per day in sub-zero cold (-30 to 0°F/-35 to -15°C).
Larger homes, leaky or thin-walled buildings, or an extreme climate will require more fuel, and thus more time, to heat. In some cases a rocket mass heater may not be enough to offset all building losses; you may need a backup heat source for really cold weather, or you may have to make some home heating efficiency improvements.
Multiple heaters are not very convenient to run unless they can be automated (or you have more operators to share the work than heaters).
If you want to heat a large home on wood alone, with minimal operator hours per day (not counting wood preparation), consider large masonry heater designs that have larger batch-burn fireboxes, or automated central heating (furnaces, boilers). They will not be as fuel efficient, but heating large spaces with small numbers of people inside is not an energy-efficient lifestyle to begin with.
For all spaces, consider ways to reduce the heating loads. Can you capture or conserve more heat? Can you cluster the heat-loving elements into a smaller space? Can you improve insulation, or close off unused closets and rooms to protect the warm core?
We have known people to keep their original furnace or woodstove, and use the mass heater to cut their overall fuel bills (often to one quarter or less of the original costs) while retaining the old heater for backup.
In general, rocket mass heaters have been most popular for small, efficient homes, in temperate to sub-arctic climates. Arctic and industrial-scale designs are beyond the scope of this book, except as noted in Appendix 3.
Firewood Takes Work
Those moving from automated heaters (furnace, heat pump, baseboard heaters) to wood heat may not realize what's involved in securing and storing dry firewood.
Dry fuel is not found in nature, nor is it found on damp ground under a tarp. Like dehydrated fruit or dry laundry, dry firewood is a product of intelligent effort. The tool for producing dry fuel wood is a wood shed. A good, dry woodshed repays the investment many times over with lower fuel costs, less work, brighter fires, safer chimneys, and easier (and cheaper) chimney maintenance.
Wood drying requirements vary by climate, but plan to store a minimum of two years' supply: half for use this year, half drying for next year (or in case of an unusually hard winter). Some varieties of wood take longer to dry.
If you currently have an almost-bigenough woodshed, a rocket heater's fuel efficiency may relieve you of the need to build a larger one. If you currently have no storehouse capable of producing or storing dry fuel, your budget for a wood-burning heater MUST include dry fuel storage. For details, see Chapter 5, and our companion booklet The Art of Fire.
Limited Flame-viewing
One of the customary perks of heating with wood is the pleasure of watching the flames. The efficient J-style firebox is intellectually amazing, but hard to watch from across the room. The operator gets the best view, though the flickering display on the ceiling can also be fascinating. Mirrors or reflective surfaces near the feed (such as a band of shiny metal trim on the barrel) can offer a reflected glow.
Ceramic glass can be used with care in some areas of the firebox; however, the glass is not as insulating as an 8" masonry and insulation sandwich, and the clean burn seems to suffer. Getting a glass-fronted door suitable to anchor in masonry (for example, from traditional oven suppliers) can add $500 or more to the project cost.
If fire-watching is a serious hobby in your household, consider a separate "fire TV" for occasional use, such as a glass-door woodstove, Rumford fireplace, or rack of candles. These low-mass space heaters can be perfect for a parlor, guest suite, studio, or formal dining room that is not used every day.
Some Spaces and Uses Are Unsuitable
Occasional-use Spaces
Thermal mass is slow to heat up and slow to cool down. It takes time and energy to shift the heater back from cold-slab mode (lovely in summer's heat) to warm-cuddly mode. If the heater mass is colder than outside air, the draft can be reluctant to start.
If you have a vacation cabin where you spend the occasional long weekend, it may not be the best place for a large masonry heater. You spend Friday night and part of Saturday in a chilly cabin bringing the mass up to temperature, enjoy the warmth briefly on Sunday morning, only to head back home on Sunday afternoon and waste the remaining stored heat.
While a rocket mass heater's radiant barrel does offer more responsive heat than most masonry heaters, making Friday night cozier, the heat in the mass is still wasted on Monday and Tuesday instead of being available for your enjoyment.
That ski cabin might be just as comfortable with a simple radiant heat source like a Rumford fireplace or woodstove. Even an inefficient woodstove or space heater may use less energy over time if heat is only needed in short bursts. In general, for heaters that will be warmed up on demand for only a few hours, we prefer a thinner mass (2" to 4"); or a lower-cost option such as a wall of brick behind a woodstove.
The same problem occurs in churches, meeting halls, retreats, and guest facilities: preheating the mass takes precious custodial time and energy, and there is the same problem of wasted heat after the group leaves the space.
Passive solar designs and climate-appropriate designs, including insulation for harsh climates, are a good investment no matter what the building's used for.
Comparing Other Heating Options
When we suggest that a rocket mass heater is not a good fit for a particular situation or goals, we are often asked about other heating options. The Heating Situation graph compares common wood-fired and energy-efficient heating choices, and the situations where they may be most useful. Alternative heating options are discussed in more detail on the energy forums at www.permies.com, www. builditsolar.com, and www.chimneysweeponline.com.
Portable Structures and Off-ground Flats
A mass heater is, well, massive. Masonry heaters are best supported on noncombustible foundations directly on the ground, in the occupied areas of the home.
If your home does not have any groundfloor occupied areas, or is a flat without permission to alter the rooms above, yours is a difficult situation for a mass heater.
Manufactured homes and portable dwellings have additional constraints: they sacrifice energy efficiency and size for convenience, and may have special code requirements for appliances.
It may be easier to build an addition (like a sunroom) onto a manufactured home, or as part of a pull-in shelter for a camper. This makes it easy to support the heater on noncombustible pad or blocks, rather than trying to support a heavy mass on a portable floor system.
We have considered some camper and boat mass-heater designs. In general, most live-aboards and campers are compact enough that insulation (like a room-sized sleeping bag) is an easier path to comfort, and far less weight to transport.
The design particulars for all of these situations are outside the scope of this book, except for Appendix 3.
Domestic Hot Water and Cooking
We enjoy cooked food and hot water yearround, while home heating is a seasonal need. Basic survival cooking can be done on top of the heater's metal bell, or hot water warmed in batches with an open tank or pot. However, providing pressurized domestic hot water is a complex design problem with potentially lethal risks. Most households should have a separate device for summer cooking and for domestic hot water. Boilers and hot water design are beyond the scope of this book, except as discussed in Appendix 3.
Table of Contents
Acknowledgments and Background vii
Chapter 1 Rocket Mass Heater Overview and Terms 1
Chapter 2 General Design Considerations 25
Chapter 3 Design Examples 39
Chapter 4 Step-by-Step Construction Example 59
Chapter 5 Operation and Maintenance 101
Chapter 6 Rules and Codes 137
FAQs 163
Appendix 1 Earthen Building 179
Appendix 2 Rocket Mass Heater Building Code (Portland, Oregon) 199
Appendix 3 Special Cases 205
Appendix 4 Home Heating Design Considerations 225
Appendix 5 Wood Heat Considerations 241
Appendix 6 Supplemental Practice Activities 257
Index 269
About the Authors 277
What People are Saying About This
"Finally - a comprehensive book about rocket mass heaters! This should put an end to the freak shows of flaming death showing up on YouTube mislabeled as rocket mass heaters. And put an end to getting the same questions asked over and over again. We can start every answer with: 'Have you read The Rocket Mass Heater Builder's Guide."
— Paul Wheaton, founder of Permies.com online community
"Eagerly awaited by homesteaders both urban and rural, appropriate tech folks, and do-it-yourselfers of all stripes, The Rocket Mass Heater Builder's Guide is a comprehensive, well-researched, and clearly illustrated manual on one of the most exciting home-heating concepts to come along in decades. The book is firmly grounded in the authors' many years of experience, will save every builder vast amounts of toil and frustration, and paves the way to a home-heating system that is clean burning, marvelously fuel efficient, and a pleasure to live with. Rich in detail without being overwhelming, this book is an essential addition to every homesteader's and builder's library."
— Toby Hemenway, author, Gaia's Garden and The Permaculture City
"An advanced companion to Rocket Mass Heaters: Superefficient Wood Stoves You can Build and Snuggle Up To. The second, more comprehensive work on revolutionary wood heating; thorough, technically advanced, comprehensive, well thought-out by the experienced masters of rocket stoves."
— Ianto Evans, director and founder, Cob Cottage Company, inventor of Rocket Mass Heaters and Lorena Stoves
"Drawing on the centuries-old tradition of masonry stoves and heaters, the "rocket" mass heater offers a modern, fuel-efficient way to heat a home with wood. This Guide represents more than ten years of collaboration and lessons learned from hands-on building and experimentation. The result is a frank, practical and detailed discussion of design and construction, pros and cons, and helpful anecdotal stories. While passionate about empowering the owner-builder, the authors also address code compliance and stress fire safety."
— Catherine Wanek, author/photographer, The New Strawbale Home and The Hybrid House, and co-author, The Art of Natural Building
"In The Rocket Mass Heater Guide, Erica and Ernie Wisner have distilled the best, most tried-and-true design for efficient, low-cost, low-effort, carbon-neutral, regenerative home heating. Undoubtedly people will continue to experiment, but it will be hard to improve upon the wisdom of this book - what works, what doesn't and why."
— Albert Bates, author, The Biochar Solution
"You will be happy to own this book for years and years to come! There are life-changing secrets inside of Erica and Ernie Wisner's most remarkable book, ways of understanding how to live better, more simply, and more beautifully while also being more snuggly and cozy that you ever thought possible."
— Mark Lakeman, co-founder, City Repair and design director, communitecture
"Over the years, a handful of dedicated practitioners and authors have helped the natural building movement advance their craft based on solid engineering and experimentation. The authors are among that elite and vital group, and this book is a must-read for anyone who longs for practical, detailed knowledge on rocket mass stoves based on extensive experience."
— Dan Chiras, Ph.D., director, The Evergreen Institute and author, The Natural House and The Homeowner's Guide to Renewable Energy
"Biomass energy is sensible when used super-efficiently and locally - which is the point of this book. Folks who live in cooler climates can benefit enormously from this simple, do-it-yourself technology."
— Richard Heinberg, Senior Fellow, Post Carbon Institute
"The Rocket Mass Heater Builder's Guide provides a remarkable amount of detail for designing, building and using these elegant and efficient space heaters. In a world of ever-diminishing resources, growing populations and changing climates, safe, efficient and low-cost solutions to space-heating without fossil fuels are vitally needed. I have long planned to build a high mass rocket stove in my bioshelter/ greenhouse to replace our woodstove. After reading this book, I feel inspired and feel confident to do it."
— Darrell E. Frey, author, Bioshelter Market Garden: A Permaculture Farm