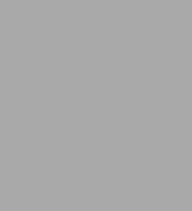
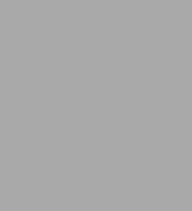
eBook
Related collections and offers
Overview
Authoritatively written and expertly arranged by a master craftsman and instructor, this volume examines in detail dozens of early tools and their functions. More than seventy drawings and photographs accurately depict—among other devices—chopping and splitting tools, hammers and knives for a variety of uses, chisels, gouges, and saws; planes and drills, vices and cramps, hole-making tools, tools for working the soil, as well as equipment for blacksmithing, spinning, weaving, and baking.
An invaluable resource for hobbyists, collectors, and museum curators, this volume will also be prized by lovers of traditional ingenuity and know-how.
Product Details
ISBN-13: | 9780486146386 |
---|---|
Publisher: | Dover Publications |
Publication date: | 08/27/2012 |
Series: | Dover Crafts: Building & Construction |
Sold by: | Barnes & Noble |
Format: | eBook |
Pages: | 224 |
File size: | 15 MB |
Note: | This product may take a few minutes to download. |
Read an Excerpt
COUNTRY TOOLS and HOW TO USE THEM
By Percy W. Blandford
Dover Publications, Inc.
Copyright © 1997 Percy W. BlandfordAll rights reserved.
ISBN: 978-0-486-14638-6
CHAPTER 1
Craftsmanship
What is a craftsman? The term embraces craft workers of both sexes. Broadly speaking, a craftsman makes things by hand and normally sees the job right through from raw material to finished product. There are exceptions, but an assembly-line worker cannot be described as a craftsman, neither can the man who operates an automatic machine churning out identical objects. Both may be exercising skill, but it is not the skill of a craftsman. In some crafts the worker uses machines in addition to hand tools, but these are under his control and he has to exercise his craft skill in controlling them. An example is the turner and his lathe. Even with a modern power-driven lathe, it is the skill of the turner which produces results. He is using the lathe as a mechanised tool. In some activities the craftsman produces parts, which someone else uses to make the final object, but the parts he makes call for craft skill and each is an individual product. For instance, one craftsman made wooden clog soles in the woodland where the wood was cut, and another craftsman made and fitted the leather uppers in a workshop. In the chairmaking industry, the final chair was the result of the efforts of several craftsmen skilled in making parts.
In many cases the craftsman was also the designer of his product. If he was working to a design by someone else, there was close liaison between designer and craftsman. It would be very unlikely that a craftsman would work to a design by someone remote from him. They would need to be in close touch. A craftsman nearly always made things one at a time. Each was unique in that it differed slightly from all other broadly similar articles which the worker produced. In this sense a craftsman was also an artist, even if he was only concerned with utilitarian products.
The oldest crafts must have originated when primitive man, roaming in woodlands, used stones in the form he found them for cutting and hitting, with branches and boughs as levers and mallets. The same implements were used as weapons for defence and killing animals. Then, as man moved on to being more static, with some tilling of the land and the erection of shelters, some were discovered to be more skilled at these jobs than others and the first craftsmen found a place in the community. They did jobs for others and received services or goods in exchange.
The system of barter, or the exchange of services and goods, continued until quite recently. There was surprisingly little money in a village while it was generally self- sufficient. The carpenter did a job for the miller in exchange for a bag of flour, which he might then exchange with the butcher for meat. The blacksmith made parts for a wheelwright, who let him have waste wood as fuel. Assessing exchange values and accounting for debts due when they accumulated over a series of jobs must have been difficult. Even the vicar was paid in kind and his tithe barn is still found in many villages. Itinerant workers and those who hawked goods from the towns would want payment, and workers visiting towns would need money, but the close community in which most country craftsmen worked got along on mutual trust and a sharing of produce.
The discovery of bronze, then iron and some of the precious metals, brought primitive man further up the scale as a craftsman. The working of metal necessitated skill greater than the ordinary man was likely to have as a mere sideline to his agricultural and domestic activities, so specialists were called for. Evidence of remains from many thousands of years ago shows that primitive man not only made serviceable things, but also decorated them, showing considerable design and artistic ability. From those early metalworkers came the smiths and jewellers.
As wood is not so durable and wooden remains have not survived as well as metal, we have less evidence of woodworking craftsmanship, but some tools have survived and woodworking craftsmen must have had the skill to use them to produce work of comparable quality to that of the metalworkers. Wood was one of the most useful materials for many branches of craftsmanship, and still is, despite the proliferation of so many plastics and other synthetic materials.
Country craftsmanship in Britain is not entirely a thing of the past, but most rural craftsmen who are still able to make a living have had to move with the times and adapt their work so as to cope with 'progress'. For thousands of years, craftsmen practised their art with little likelihood of something revolutionary taking away their job. From long before the birth of Christ, country carpenters, smiths, masons, weavers and other craftsmen continued with little change, knowing that their job was secure in their community. There was a need for them and they thought there always would be. Son followed father, being assured of a place and an opportunity to earn a living at his craft. Up to the eighteenth century, the country craftsman carried on a job and served a need which his counterpart of several centuries before would have recognised. Even his tools were very similar.
So long as man was a local animal this condition survived. A few adventurers travelled and brought back ideas, but they were the exception. The conditions of roads made travel difficult. A few miles to a market town in summer was quite an adventure. The same journey in the winter was usually impossible. Then transport improved: roads were made better. At the end of the eighteenth and beginning of the nineteenth century, there was a fever of canal building. By linking navigable rivers, canals made possible the transport of heavy goods over longer distances. Coupled with this was the development of industry. Factories in the Midlands began making goods that had previously been the preserve of the country craftsman. They began producing tools which previously the smith had made.
The canals were closely followed by the railways - too closely to enable the canals to become successful and many did not survive. The network of railways brought communication to a bigger area, with the transport of people and goods being comparatively easy, so that people moved out of their village, either on visits or to work in the industrial developments which were crying out for labour. Instead of the community being self-contained, products from one part of the country were exchanged for those from another part. One part of the country began to specialise in a particular product and trade this for the products of other parts.
Even in medieval Britain, there were certain things for which a village could not be self- sufficient. Not many smiths could get their iron locally. Some of it came from the Weald of Sussex. More came from the Forest of Dean. Some came from the Severn Valley. The bridge at Ironbridge, still there, was cast locally in 1777, and the town named after it. Cloth, other than the locally woven wool, might come in via pedlars from Lancashire or elsewhere, and pottery from the Stoke-on-Trent area.
One interesting example of what must have been early quantity production was the supply of staddle stones - the mushroom-like stones used to support barns or ricks so that rats could not climb up (Photo. 1–1). These could have been made locally, but they were made in large quantities in the eighteenth century or earlier at the quarries at Portland and Purbeck, then shipped around the coast to ports where they were bought and carried inland to sell to farmers.
Most craftsmen were occupied satisfying the needs of people in the locality, but in this way they were doing little more than supplying a utilitarian product, with little scope for artistry or the development of greater skills and higher degrees of craftsmanship. The customers could do no more than pay for the essentials. Fortunately, some craftsmen were able to obtain patronage, which ensured them an adequate return while they produced articles of better quality. For many centuries the church was the largest source of patronage for promising craftsmen, so some fine examples of early craftsmanship in wood, stone, iron and precious metals are in ecclesiastical buildings.
Royalty and nobility also provided patronage. As the wealth and power of the church waned, this coincided with the growth of a class of wealthy merchants and traders, many of whom spent some of their wealth on the acquisition of furniture, gates and other examples of good craftsmanship, so the better craftsmen were able to use their tools on worthwhile projects.
Progress moved at a snail's pace for centuries. The order of things differed little over a thousand years, then in just over a century the way of life changed for most of the world. Little wonder that the country craftsman almost disappeared. Fortunately, one reaction to mass production is a realisation of the quality and attraction of individually made articles, so those craftsmen able to satisfy this demand are able to keep their workshops going. The smith has little call for shoeing horses, but if he can make wrought iron gates as a quality product, there is a demand for them. Potters, in comparatively large numbers, are able to find customers. In other crafts, some of the small numbers who have not deserted their workshops for the probably better financial returns of a soul-destroying job in industry are finding satisfying work in filling a demand now that competition is reduced. Saddlers have plenty of work. Farmers find there is no satisfactory modern alternative to the hurdle, so hurdlemakers have employment.
Broadly the country craftsmen could be divided into several groups, mainly according to where they did their work. Those who worked in the woodland converted wood as they cut and moved on when the local supply was exhausted. The chair bodger in the beech woods was one of these. Despite the need for a lathe, his entire tool kit, including the vital bits of the lathe which could not be improvised locally, was very small. Similarly, the clogger, hoopmaker and others who cut spars and poles had very few tools. Next was the group of craftsmen who took the cut coppice wood to a workshop or yard and processed it there. People like the broom squire, rakemaker and gate hurdle-maker had some homemade appliances set up, but their tools were not much more numerous than those of the first group.
Those craftsmen did work which called for little precision. A variation of an inch or so did not matter. Those who had to work more accurately needed an indoor workshop, usually with one or more substantial benches with reasonably true tops. They all needed fairly comprehensive tool kits. While the coppice worker or the one who took the wood to a yard might double at more than one trade according to needs, the craftsman who needed a workshop was more of a specialist and needed greater skills. It was these workshop trades for which apprenticeships were served and trade secrets were jealously guarded. The smith was one of these specialists, with a place for at least one in every village. The carpenter was another. Although a specialist in one sense, he was expected to tackle an infinite variety of jobs. The wheelwright was even more of a specialist. Both these woodworkers needed quite large tool kits, their value representing a fair amount of a man's entire property. The cooper was another specialist woodworker, with a rather different range of tools, who might serve several villages.
Those who worked in stone and clay might be comparatively low-grade craftsmen, doing walling and making bricks, and needing few tools. The mason capable of decorative work in stone was more likely to be based in a town or itinerant, moving to where his skill was required. His tools tended to be heavy, so he probably had a cart or pack-horse.
The saddler was supposed to need more tools than any other country craftsman. There was certainly a need for him to deal with harness and saddlery in every village.
Most craftsmen had their workshop set up adjoining their home. No one went very far to work. Some did their job in their home. Spinning was a usual activity for women and looms for weaving were also set up in the home. Most static craftsmen could be said to live on the job which often meant working long hours. There were fewer distractions to take a man away from his work, but as most workers were self-employed and liked to describe themselves as mastermen, and incomes from their craft depended on how much work they did, there was an obvious incentive to keep at it. Even then, the return from the work was not much, by present day standards, and the agricultural workers fared even worse.
It is interesting to see that the development of crafts followed very similar patterns in other parts of the world although at different paces. In America, of course, craftsmen emigrated from Europe and the need for specialists in the various trades was met in American pioneering days in the same way as in Britain. Improved transport and communications, with possibly a quicker industrialisation, killed country craftsmanship more definitely there than in Britain. The lack of individual craft skills is now seen in the demand for craft products in America from Britain and the rest of Europe.
European progress has been much the same as in Britain, although some countries have hung on to craft skills. For instance, wood carving is still a profitable cottage industry in parts of Switzerland, Austria and Germany. Much of the craftwork developments in Britain came with the Roman invasion. At that time, around the birth date of Christ, much of Europe was under Roman domination so crafts of similar types and techniques were started in those parts of Europe which formed the Roman Empire.
Elsewhere it is possible to see craftwork developments several centuries behind our own experience. In India excellent woodwork and metalwork is being done with most primitive tools and equipment. In many parts of Africa the natives are trying to move from something like the Stone Age to the Atomic Age in one generation, so primitive tools are still found in use not far from the most modern machinery. In Japan the whole process may be seen taken to what might be called its illogical conclusion, with all pretence of individual craftsmanship giving way to all-out industrialism.
Craftsmen today, who are able to make a living at their craft, have had to adapt to modern ways with power tools. There is no virtue, and certainly no profit, in laboriously hand- planing wood to thickness when a planer/thicknesser will do it quickly and accurately. An electric router can save a lot of hand work in cutting joints, rabbeting and moulding. Holes in metal are easy to make with an electric drill, but hard work to make by hand.
Today, a conscientious craftsman, in any medium, uses power tools to lessen labour and obtain mechanical accuracy, but the vital work in his project is the result of his skill and artistry mainly with hand tools. Signs of power tool preparation are hidden by subsequent hand work. We hope modern exponents of country crafts will long continue, but this book is not about power tools.
CHAPTER 2Axes
Primitive man probably picked up a stone with a sharp edge and used it both as a weapon and as a tool for skinning animals, splitting wood or digging soil. He would soon discover that some stones were more suitable and would keep sharp strong edges, while others were weak and would crumble. Flint proved to be his standby in North America, Wales and other places where he could find it. It may not have been long before he discovered that he could get more power into a blow by fixing the stone to a handle. The mechanics of it may have been beyond him, but having the heavy head further from the fulcrum of his wrist, elbow or shoulder, allowed the cutting edge to be brought down with more force. And so the axe was born.
Lashing the stone head to a wood shaft was obviously not very satisfactory, although that must have been the first method used. As skill developed, the shaft was put through a hole in the axe head. Making a hole seems to have been achieved quite early in tool history, possibly by slow work with another stone. This may be seen in examples discovered, such as the olerine dolerite axe head of the late Bronze Age, about 1000 BC, in the museum at Wookey Hole. Although worn away by water, it was obviously quite a good shape (Fig. 2-1A). This is still the most favoured method of attachment, although the risk of the parts separating, with possible dire consequences, has not yet been completely eliminated.
In the Middle Ages some country craftsmen may not have had the skill to put a hole in a steel axe head. An alternative was to wrap the steel of the head around the shaft, making a folded socket, secured by rivets - not such a workmanlike method, but apparently satisfactory (Fig. 2-1B).
(Continues...)
Excerpted from COUNTRY TOOLS and HOW TO USE THEM by Percy W. Blandford. Copyright © 1997 Percy W. Blandford. Excerpted by permission of Dover Publications, Inc..
All rights reserved. No part of this excerpt may be reproduced or reprinted without permission in writing from the publisher.
Excerpts are provided by Dial-A-Book Inc. solely for the personal use of visitors to this web site.
Table of Contents
Contents
Title Page,Copyright Page,
Table of Figures,
Introduction,
Chapter 1 - Craftsmanship,
Chapter 2 - Axes,
Chapter 3 - Mallets and Hammers,
Chapter 4 - Knives,
Chapter 5 - Chisels,
Chapter 6 - Saws,
Chapter 7 - Planes,
Chapter 8 - Making Holes,
Chapter 9 - Holding and Handling,
Chapter 10 - Measuring and Marking-Out,
Chapter 11 - Turning and Round Work,
Chapter 12 - Rural Engineering,
Chapter 13 - Agricultural Hand Tools,
Chapter 14 - Fabric and Fibrous Crafts,
Chapter 15 - Other Tools,
Appendix 1 - Hardening, Tempering and Annealing,
Appendix 2 - Tool Sharpening,
Appendix 3 - Timber,
Appendix 4 - Craft Names,
Bibliography,
Index,