Cooling Techniques for Electronic Equipment / Edition 2 available in Hardcover
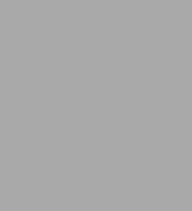
Cooling Techniques for Electronic Equipment / Edition 2
- ISBN-10:
- 0471524514
- ISBN-13:
- 9780471524519
- Pub. Date:
- 04/16/1992
- Publisher:
- Wiley
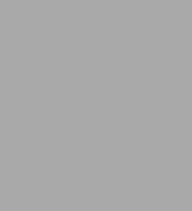
Cooling Techniques for Electronic Equipment / Edition 2
Hardcover
Buy New
$293.95Buy Used
$174.51-
-
SHIP THIS ITEM
Temporarily Out of Stock Online
Please check back later for updated availability.
-
Overview
Product Details
ISBN-13: | 9780471524519 |
---|---|
Publisher: | Wiley |
Publication date: | 04/16/1992 |
Edition description: | REV |
Pages: | 512 |
Product dimensions: | 6.48(w) x 9.39(h) x 1.37(d) |
About the Author
Read an Excerpt
Chapter 1: Evaluating the Cooling Requirements
1.5 Electronics Equipment for Airplanes, Missiles, Satellites, and SpacecraftElectronic boxes used in airplanes, missiles, satellites, and spacecraft often have odd shapes that permit them to make maximum use of the volume available in oddshaped structures. An odd-shaped box may require more time to design, because it is usually more difficult to provide the circuit cards with an efficient heat flow path, regardless of the cooling method used.
The trend in military and commercial airplanes and helicopters is toward a series of several standard sizes for plug-in types of electronic boxes that fit in racks. These are called ATR (air transport rack) boxes. They are of various widths, which are known as one quarter, one half, three quarters, and full width, each with a short and a long length. The electrical interface connectors are often at the rear of the box, with quick release fasteners at the front [1].*
Many of the electronic boxes are cooled by forced convection with bleed air from the jet engine compressor section. Since this air is at a high temperature and pressure, it is throttled (passed through the cooling turbine), cooled, and dried with a water separator before it is used. This air often enters the electronic box at the rear, adjacent to the electrical connectors. Rubber gaskets are used around the inlet ports at the air interface to provide an effective plug-in connection, which reduces the leakage at the cooling air interface.
Sometimes the conditioned cooling air is not completely dry because of excessive moisture in the air from humidity or a rainstorm. Small drops of water will often be carriedinto the electronics section together with the cooling air. If this water accumulates on PCBs or their plug-in connectors, electrical problems may develop. Therefore, many specifications do not permit external cooling air to come into direct contact with electronic components or circuits.
Air-cooled heat exchangers, commonly called air-cooled cold plates, which are being used more and more in airplanes, provide conditioned air for cooling the electronics. These heat exchangers are usually dip-brazed when many thin [0.006 to 0.008 in (0.15 to 0.20 mm)] aluminum plate fins are used. Pin fin aluminum castings are becoming very popular because of their low cost. There is usually a slight weight increase with pin fins because the walls and fins have to be thicker to permit the molten aluminum to flow [2, 3].
Electronic systems for missiles generally have two cooling conditions to consider, captive and free flight. If the missile flight duration is relatively short, the electronics can be precooled during the captive phase so that the system can function with no additional cooling during the flight phase. The electronic support structure would act as the heat sink, soaking up the heat as it is generated, to permit the electronic system to function during the free flight phase.
Some missiles, such as the Cruise missiles, have a very long free flight phase, so that the cooling system must be capable of cooling the electronics for several hours. If ram air is used at speeds near Mach 1, the ram temperature rise of the cooling air may exceed 100°F (55°C). Since Cruise missiles fly at low altitudes, where the surrounding ambient air temperatures can be as high as 100°F, the cooling air temperatures could reach values of 200°F (93°C) even before the cooling process begins. Since the maximum desirable component mounting surface temperature is about 212°F (100°C), the outside ambient air cannot be used directly for cooling.
Cruise missiles must carry a large supply of fuel for their long flights. The fuel is often pumped through liquid-cooled cold plates to provide cooling for the electronics. Toward the end of the flight mission, when the fuel supply runs low, the temperatures may increase. At this point it may be necessary to use the thermal inertia in the electronics structure to keep the system cool enough to finish its flight.
Electronic systems for satellites and spacecraft generally rely upon radiation to deep space for all their cooling. Deep space has a temperature of absolute zero, -460°F or 0°R (-273°C or °K). Temperatures this low can provide excellent cooling if the proper surface finishes are used [4].
Special surface finishes and treatments may be required for satellites and spacecraft to prevent them from absorbing large quantities of heat from the sun. This heat may be direct solar radiation plus solar radiation reflected from the various planets and their moons (reflected radiation is called albedo) [4, 5].
Liquid-cooled cold plates are often used to support electronic systems. Pumps then circulate the cooling fluid from the cold plates, where the heat is picked up, to the space radiators, where the heat is dumped to space.
Conduction heat transfer is used extensively for cooling electronic equipment in space environments. In the hard-vacuum conditions of outer space, flat and smooth surfaces must be utilized with high contact pressure to minimize the temperature rise across each interface. Although air is not normally considered to be a good heat conductor, its presence will sharply reduce the contact resistance at most interfaces. Thermal greases are sometimes used to reduce the interface resistance in hard vacuum environments, by filling the small voids that would otherwise develop when the air is evacuated.
Air cooling can still be provided in a hard-vacuum environment if a sealed and pressurized box is used. An internal fan can be used to circulate internal cooling air through a liquid-cooled cold plate, which would carry away the heat. The heat from the fan must be added to the total heat load of the system. Also, a sealed box will have a large pressure differential across the surfaces of the box in the vacuum of outer space. The outer surfaces of the box must therefore be thick and stiff to resist excessive deformations and stresses caused by these pressures.
Natural convection cannot be used to transfer heat in satellites and spacecraft electronics. Natural convection requires a gravity field to permit the heated air to rise, because of its reduced density. In satellites and spacecraft, the effects of gravity are neutralized by the velocity and the continuous free-fall characteristics of the flight path. Therefore, only radiation, conduction, and forced convection (in sealed boxes) should be considered for cooling electronic systems in space.
1.6 Electronic Equipment for Ships and Submarines
Large cabinets, consoles, or enclosures are normally used to support the electronic equipment used on ships and submarines. These cabinets are usually heavy and rugged, to provide protection for the electronics during storms and rough seas. Some cabinets may dissipate more than 2 kilowatts of heat, so liquid-cooled cold plates and heat exchangers are often used to cool the equipment. The electronic components are often mounted on panels and sliding drawers. Panels are used to support displays, and drawers are used to support the heavy power supply units. Completely enclosed cabinets are often used by the Navy with special radio frequency interference (RFI) and electromagnetic interference (EMI) gaskets on heavy doors. This protects and shields the electronics from undesirable radiated and conducted electromagnetic waves, which can interfere with the operation of the equipment. Because these systems are completely enclosed, cooling problems may become quite severe [6].
Water is usually available on ships and submarines, so that it is natural to utilize it for cooling. Water-cooled heat exchangers are often used, with external fins to permit cooling with forced air. Fans are used to force the air through the heat exchanger fins to cool the air, which is then circulated through the console. This type of forced convection cooling can be used with both closed-loop and openloop systems. With a closed-loop system, a cooling air supply plenum and a return plenum may be established within the sidewalls of the consoles. The sidewalls are often several inches deep, with ribs to provide rigidity from high shock loads, so that they can easily carry the cooling air to and from the electronics. If an openloop system is used for cooling, the air entering the console would be forced through the water-cooled heat exchanger, which is usually at the base of the console. The conditioned air would be circulated through the electronics and then exhausted at the top of the console.
When the heat loads are not too high, natural convection techniques can often be used to cool the electronics. This works well on tall cabinets, which can use chimney effects to force the air through the system without the use of fans or pumps. Air enters at the bottom of this cabinet, where it first picks up heat from the electronics. The warmer air has a reduced density, so that it starts to rise through the chassis, picking up more heat as it rises. The cooling air finally exits at the top of the cabinet...
Table of Contents
Evaluating the Cooling Requirements.Designing the Electronic Chassis.
Conduction Cooling for Chassis and Circuit Boards.
Mounting and Cooling Techniques for Electronic Components.
Practical Guides for Natural Convection and RadiationCooling.
Forced-Air Cooling for Electronics.
Thermal Stresses in Lead Wires, Solder Joints, and PlatedThroughholes.
Predicting the Fatigue Life in Thermal Cycling and VibrationEnvironment.
Transient Cooling for Electronic Systems.
Special Applications for Tough Cooling Jobs.
Effective Cooling for Large Racks and Cabinets.
Finite Element Methods for Mathematical Modeling.
Environmental Stress Screening Techniques.
References.
Index.