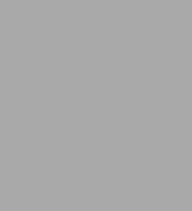
Boatowner's Mechanical and Electrical Manual: How to Maintain, Repair, and Improve Your Boat's Essential Systems
832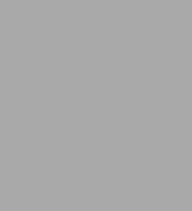
Boatowner's Mechanical and Electrical Manual: How to Maintain, Repair, and Improve Your Boat's Essential Systems
832eBook
Related collections and offers
Overview
The boatowner's foremost troubleshooting guide, now better than ever
If it's on a boat and it has screws, wires, or moving parts, it's covered in Boatowner's Mechanical and Electrical Manual. When you leave the dock with this book aboard, you have at your fingertips the best and most comprehensive advice on:
- Battery technologies
- 12- and 24-volt DC systems
- Corrosion, bonding, and lightning protection
- Generators, inverters, and battery chargers
- Electric motors and electric lights
- Marine electronics, antennas, and RFI
- Diesel engines
- Transmissions, shaft brakes, and propellers
- Refrigeration and air-conditioning
- Tanks, plumbing, and through-hulls
- Pumps and watermakers
- Steering, autopilots, and wind vanes
- Stoves and heaters
- Winches, windlasses, and bow thrusters
- Spars, rigging, and roller reefing
"If you had to choose a single book to help you assess and maintain your boat gear, this would be it."—Practical Sailor
"A truly remarkable bible. . . . This book is the best of its kind."—WoodenBoat
"A major achievement. . . . It would be hard to imagine anything going wrong on a boat that couldn't be figured out with this book."—Sailing World
"The world's best technical reference and troubleshooting book."—Sailing Inland and Offshore
"This manual will be of lasting interest to anyone who wants to know how their boat works, what has gone wrong when it doesn't, and how it could be fixed."—Classic Boat
"Without becoming too complex, the book covers almost every imaginable mechanical or electrical matter in the marine environment."—Work Boat World
"Calder lives what he writes, . . . [and] what he offers . . . is practical solutions to problems associated with increasingly complex marine systems. . . . [A] bargain for anyone in the construction and repair side of the boat business."—Professional Boatbuilder
Product Details
ISBN-13: | 9780071784061 |
---|---|
Publisher: | McGraw Hill LLC |
Publication date: | 06/21/2005 |
Sold by: | Barnes & Noble |
Format: | eBook |
Pages: | 832 |
File size: | 78 MB |
Note: | This product may take a few minutes to download. |
About the Author
Nigel Calder is widely acknowledged as the world's foremost writer on boat systems maintenance. He is a frequent contributor to boating magazines in the United States and Britain.
Read an Excerpt
Boatowner's Mechanical and Electrical Manual
By Nigel Calder
McGraw-Hill
Copyright © 2005 Nigel CalderAll right reserved.
ISBN: 978-0-07-178406-1
Chapter One
Establishing a Balanced Battery-Powered Electrical System
Introduction
Today's pleasure boats have become increasingly dependent on electricity. Very few engines can be started without it; an increasing number of boatowners can't navigate without it; and a lot of toilets can't even be flushed without it! While the explosive growth of electrical and electronic equipment over the past decade or two has brought about a revolution in comfort and ease of boat handling, electrical malfunctions have become the most common maintenance problem aboard boats, especially those with aging, hodgepodge, or jury-rigged electrical circuits.
The marine environment is a terrible place for electricity. To be trouble free, electrical circuits must be installed with great care and to the highest standards—topics that are dealt with in Chapter 4. But no matter how carefully an electrical installation is carried out, the entire system must be properly balanced in the first place, or it will soon become a source of endless problems and a constant drain on the pocketbook.
Because of improperly set up systems, many boatowners repeatedly find themselves with dead batteries, outright battery failures, and lengthy charging times. Fixing immediate problems does nothing to resolve the overall imbalance in the system, guaranteeing that the next difficulty is just around the corner. A large number of boats come straight off the production line with these potential problems built in. Thus the first requirement for electrical problem solving and repair is to understand the peculiar needs of a boat's DC electrical system and to make sure the overall system is in balance. This Chapter takes a look at these general considerations; Chapter 2 looks at more complex systems; and Chapter 3 deals with detailed maintenance, troubleshooting, and repair procedures for specific pieces of DC electrical equipment. Although I focus on 12-volt systems, all information is equally applicable to 24 or 32 volts.
The Peculiarities of Boats
Consider first an automobile. A 12-volt battery provides the energy to crank a starter motor, normally for just a second or two, after which the engine fires up and the alternator cuts in. The alternator subsequently supplies all the car's electrical needs, plus an extra margin to replace the energy the starter motor withdrew from the battery. The car's electrical system runs on the power supplied by the alternator, not that supplied by the battery. Although starter motors use a tremendous amount of energy, they do so for a very brief period of time, and thus pull next to nothing from a battery. For example, a 400 amp starter motor (a large starter motor) would consume 400 amp-hours of energy in 1 hour, but cranking it for 15 seconds (which is far longer than normal) drains the battery by only 400/(4 × 60) = 1.66 amp-hours, which is not very much! (The distinction between amps and amp-hours is drawn on page 13.) This drain is replenished by the alternator in just a few minutes. Under normal use, a car battery is almost always fully charged, and the batteries do very little work. This holds true for almost all cars, regardless of size, electrical complexity, or use. (The exceptions are some hybrids in which the engine shuts down when stationary in traffic, and the car systems temporarily run off the batteries.) In general, the only variable from one car to another is the capacity of the alternator—cars with high electrical loads need bigger alternators.
Contrast this first with a sailboat. The average boat spends most of its time in a slip. Periodically the owner cranks the engine, motors out of the slip, shuts the engine down, and goes sailing. Apart from the time spent motoring, the boat's electrical system runs directly off the battery. The battery will be discharged more deeply than an automobile battery, while the engine will be run far less than an automobile engine, providing minimal charging time.
Now consider the average powerboat. The engine will be run for longer periods of time than a sailboat's, with usage patterns often similar to those of an automobile. But even so, many powerboats, especially cruising boats (notably trawler yachts), will have extended periods when the engine is shut down, and the boat's electrical system is running off the batteries. Although larger powerboats may have a 24-hour-a-day generating capability, with a battery charger left permanently on so that battery service closely resembles that of an automobile, this scenario is not necessarily the norm (and in any case, is often a poor way to design a system—see Chapter 2). An increasing number of boatowners with onboard AC generators and substantial power requirements are discovering that with a DC-to-AC inverter (see Chapter 6), they can shut down their generators for most of the day, enjoying peace and quiet while on the hook and saving money at the same time. In this case too, battery use closely resembles that of cruising sailboats.
What this all adds up to is that in contrast to automotive use, at some point in time almost all boats run their DC systems off the battery, deeply discharging it. As a result, the working environment for all the major DC system components—the battery, alternator, and voltage regulator—is very different from that found in the automotive field, and yet, primarily for reasons of cost, it has been customary to use transplanted automotive equipment in marine applications with little or no modification. Not surprisingly, this leads to numerous problems, most of which have their origins in the limitations of existing battery technology. To see why this is so, and how to correct problems, we need to delve into this technology.
Batteries
How They Work
A battery is composed of one or more cells (Figures 1-2A and 1-2B). Each cell contains alternating negative and positive plates, between which are plate separators (insulators). All the negative plates are connected together, as are all the positive plates. Each plate has a grid configuration, and within the grid is bonded the plate's active material (Figure 1-3). The grid provides the physical structure for the plate and the means for conducting electrons in and out of the plate. The active material is the substance that produces the electrons.
When fully charged, the active material in the negative plates is pure sponge lead; in the positive plates, it is lead dioxide. The plates are placed in contact with a solution of sulfuric acid (the electrolyte). As a battery discharges, the acid from the electrolyte combines with the active material in the battery plates, forming lead sulfate and water, the latter diluting the acid solution. When a battery is charged, water is driven from the acid solution, increasing the strength of the electrolyte, while the used portion of the plate material that formed the lead sulfate is reconverted to active material.
The formula describing this process, for those who are interested, is as follows:
PbO2 + Pb + 2H2SO4 ↔ 2PbSO4 + 2H2O.
Voltage, capacity, and rate of discharge/recharge. Regardless of plate size, construction, or numbers of plates in an individual cell, any charged lead-acid cell will produce a voltage of around 2.1 volts. This is simply the voltage that results from placing lead dioxide and lead in sulfuric acid. (Cells using other metals and electrolytes have different voltages; for more on this phenomenon see the section on galvanic corrosion in Chapter 5.)
What is not built into the cell chemistry is the capacity of a cell (how many electrons the cell can store), how fast the cell can deliver these electrons when connected to a load, and how fast it can be charged.
Crudely speaking, capacity is a function of the amount of lead in a cell—the greater the weight of lead dioxide and lead paste, the greater the storage capacity. A large, thick plate will produce the same voltage as a small, thin plate, but will store many times more electrons.
The ability of a plate to give up its stored energy depends on the ability of the acid in the electrolyte to react with the active material in the plate. The active material is made porous so that the acid can filter (diffuse) through the plate, allowing water to percolate out and fresh acid to percolate in during discharges, and the reverse to happen during charges. The thicker the plate and the denser the active material, the slower the process of percolation, and as a result, the slower a battery will give up its stored energy, and the slower it can be charged.
When a battery is put under a heavy load, the electrolyte will first react with the accessible (surface) areas of the plates. But once these have given up their stored energy, the rate at which electrons can be released from the inner areas of the plates slows down, causing the voltage to fall off. This does not necessarily mean that the battery is dead. If you rest it, allowing time for the water to diffuse out of the plates and fresh acid to filter in, the voltage will recover as fresh areas of active material are brought into service. This is why, if a car is cranked until the battery dies and then left for a short period of time, the battery will frequently recover and crank the engine again—the acid has diffused to unused portions of the plates, providing a fresh burst of energy.
When it comes time to charge, the charging current will first reconvert to active material the lead sulfates most accessible to the electrolyte—that is, those on the surface of the plates. This can be done relatively quickly. Thereafter the rate of charge will be limited by the speed with which acid can filter out of the active material and water can filter in as the charging progresses. It is this diffusion rate that determines the charge acceptance rate of a battery. Thick-plate, high-density-active-material batteries have a lower charge acceptance rate than thin-plate, low-density-active-material batteries.
Electrolyte Variations
The electrolyte in a battery may take different forms. These differences, in turn, will affect the nature of the battery's construction. The principal variations are:
Wet or flooded electrolyte. The traditional battery has a liquid electrolyte and is known as a wet, or flooded-electrolyte, battery. During periods of charging, particularly the final stages of charging, some of the charging current breaks down the water in the electrolyte into its component parts of hydrogen and oxygen, which then bubble out of the electrolyte—the battery is said to boil or gas—lowering the level of the electrolyte. This water must periodically be replaced by topping off the battery cells with distilled water via removable vent caps.
Much of this water loss can be prevented by fitting Hydrocaps (from Hydro-Cap, 305-696-2504). These devices contain a catalyst that causes the hydrogen and oxygen to recombine into water. However, because they tend to trap heat in the battery, Hydrocaps have to be used with caution on the kinds of fast-charging systems I will be discussing later in this Chapter. In general, when they are most needed—on systems that are driven hard and experience significant water loss—they should not be used. They should never be used when equalizing or conditioning a battery (see later); if not removed, they can get hot enough to melt. (Anytime a Hydro-cap is too hot to hold, it is being used in an inappropriate application and should be removed; on the other hand, if it does not get warm during the final stages of charging, it is not working.)
Another device that reduces water loss is the Water Miser Safety Vent Cap (made by Kyocera Solar, kyocerasolar.com, and available from many alternative energy suppliers), a replacement battery cap that contains polymer beads. The beads cause some of the condensates driven out of a battery to recondense and drip back in, typically reducing water loss by about 30%. A Water Miser Cap can be left in place when equalizing.
Note that the battery plate grids in wet batteries have small amounts of antimony added to the lead during their manufacture. Antimony strengthens the grid and helps to lock the active material in the grid (which reduces shedding—see below), but it has the undesirable side effect of intensifying gassing during charging, and it promotes internal galvanic currents within a battery, which slowly discharge the battery when it is left idle (a process known as self-discharge).
Gelled electrolyte. In a gel-cell, the electrolyte is in the form of a gel with the consistency of soft candle wax. During manufacture this gel is pasted onto the battery plates and separators, which are then packed tightly together (Figure 1-4). During discharges and charges, the active material in the battery reacts with the gel in immediate contact; however, there is not the same fluid movement within the electrolyte as in a wet battery. As a result, the battery plates must be kept relatively thin to achieve adequate diffusion of the gel around them. In use, the gel can develop voids or cracks that leave areas of the plates dry and result in a progressive loss of capacity.
The gel cannot be replaced during service, so gelled batteries cannot be topped off. They are built as sealed no-maintenance units. Because they cannot be topped off, it is essential to minimize gassing during charging, since this would cause the electrolyte to dry out (it leaves a powder) and the battery to fail. Several methods are used to keep gassing to a minimum:
1. Charge voltage is carefully controlled to prevent overcharging.
2. The antimony used to reinforce conventional battery plates is replaced with calcium. The resulting plate grid is not as strong, but is far less prone to gassing or self-discharge.
3. Some batteries are allowed to build up a certain amount of internal pressure. Under pressure, small amounts of hydrogen and oxygen produced during charges will recombine into water and be absorbed into the electrolyte (as a result, these batteries are sometimes called recombinant). Excessive charging, however, will cause excessive amounts of hydrogen and oxygen to be produced, so recombinant batteries always have pressure relief valves to vent excess gases. For this reason, gel-cell batteries are also sometimes called SVR (sealed valve regulated) or VRLA (valve regulated lead acid) batteries. Anytime venting takes place, the electrolyte is drying out and battery life is being reduced (Figure 1-5).
Note that many so-called maintenance-free batteries are in reality nothing more than wet batteries with excess electrolyte contained in partially sealed cases. During service the excess electrolyte is slowly used up. Because there is no way to top off these batteries, once the plates begin to dry out they are doomed. So it is important to distinguish between these batteries and a true no-maintenance battery—i.e., an SVR or VRLA, recombinant, gelled-electrolyte battery.
Starved, or absorbed, electrolyte. A starved or absorbed electrolyte battery, generally known as an AGM—absorbed glass mat—battery, is a variation of an SVR/VRLA battery, in which the electrolyte is held in place by the capillary action of a sponge-like mass of matted glass fibers (Figure 1-6). The principal difference from a gel-cell is that the electrolyte is in a liquid, not a gelled, state. This liquid state enhances electrolyte migration in and out of the battery plates and minimizes void formation. The result is improved performance when confronted with high charges and discharges and extremely cold environments.
Modes of Failure
With these basic facts in hand, we can understand the main reasons why batteries fail. Such an understanding is essential to designing DC systems that will be free from premature failure, and in troubleshooting problem systems. The principal causes of failure are:
Shedding of the active plate material. When a battery is discharged and charged, the chemical processes in the plates—converting sponge lead and lead dioxide to lead sulfate and back again—tend to weaken the bond between the active material and the plate grids. Every time a battery is discharged, some of the active material is loosened and shed from the grid, reducing the overall capacity of the battery (Figure 1-7). This is the normal aging process and will eventually result in complete battery failure, either through material building up in the base of the battery until it reaches the level of the plates and shorts them out (Figure 1-8), or through the loss of so much active material from the plates that the battery no longer has the capacity to carry out its tasks. (Note that in recent years, more and more batteries have been built with envelope plate separators, which are sealed on the sides and bottom, so that any shed material remains in the envelope. This reduces the incidence of plate shorting, but not the shedding itself.)
(Continues...)
Excerpted from Boatowner's Mechanical and Electrical Manual by Nigel Calder Copyright © 2005 by Nigel Calder. Excerpted by permission of McGraw-Hill. All rights reserved. No part of this excerpt may be reproduced or reprinted without permission in writing from the publisher.
Excerpts are provided by Dial-A-Book Inc. solely for the personal use of visitors to this web site.